Powder piloting - Material solutions from powder to product
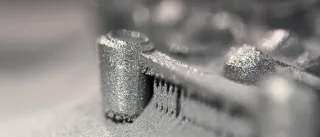
What if you could tailor your materials and manufacturing processes to create new, cost-efficient solutions against wear, corrosion and high temperatures? Or you could improve the reliability and lifetime of cutting tools by replacing traditional, hard metals with more environmentally friendly materials? What if you could utilise lathe chips as high value products and create new, sustainable business at the same time? VTT PowderPiloting enables all that and much more.
VTT PowderPiloting in a nutshell
Easy and reliable
We provide a one-stop solution for developing and evaluating the feasibility of new materials, process ideas and inventions.
We provide the right infrastructure and expertise in one location.
Fast and confidential
You’ll get your first results within a few weeks. Iterative development approach is ensured through close dialogue before, during and after the project.
All results are confidential.
Tangible results
We offer pilot-scale production for market validation and cost structure and feasibility verifiication.
We can provide the evidence you need to assure your customers.

VTT’s powder process design services
For over three decades, VTT has researched and developed new material solutions. Our capabilities range from powder processing to post treatment and characterisation.
All that experience has been synthesised into VTT PowderPiloting – a material solution service that takes you from powder to product with ease.
With VTT PowderPiloting, you can boost your development from early-stage feasibility studies and pilot scale processing all the way to the production of powder-based materials and components. We can also support you in the adoption of resource efficient manufacturing practices and the substitution of critical raw materials with alternative materials.
VTT PowderPiloting acts as an extension to your R&D organisation. It aims to strengthen your company’s capabilities, allows you to focus on your core competences and accelerates time to market.
PowderPiloting helps you design anything from coatings to components to functional additives to circular economy solutions.
New, advanced materials provide solutions to global challenges
Rising raw material costs, stricter regulations and sustainability goals drive the need for new material solutions that don’t compromise the lifetime performance. Innovative new materials address these concerns while unleashing new opportunities for a wide range of sectors from manufacturing to metal to mining and beyond.
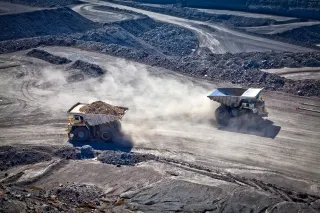
Customer success stories
Millidyne - Optimised processes leads to new products
With VTT's expertise, Millidyne was able to extend their product portfolio and commercialise a new product under the Neoxide® trademark in the HVOF ceramic coatings market.
Exote - Protection against wear and corrosion at high temperatures
VTT collaborated with Exote to create new nanoalloy-based material solutions for wear and corrosion protection also at high temperatures.
Renotech - Fireproof ceramics raw material from steel industry sidestream
Renotech and VTT developed a method for replacing part of fireproof ceramics raw material with steel industry slag. This provided Renotech with a new alternative raw material that is economical and circular.
Interested? We'd be happy to discuss more cases - contact us!
Our solutions for different industries
Coatings
- Using nano structured carbide powder to substitute hard chromium coatings in thermal spraying
- Designing a ceramic coating with enhanced ductility to protect valves
- Designing a composite coating to control chlorine corrosion in waste incineration boilers.
Components
- Designing a high temperature oxidation and erosion resistant material and burner component for a power plant
- Designing wear parts for mining applications based on novel hard metals that are critical raw material-free
- AM of soft magnetic alloys for electric machines.
Functional additives
- Designing catalytic powders for fuel cells
- Designing magnetically modified powder additives for radar absorbing coatings
- Reinforcing powder additives for metal castings
- Designing self-lubricant powders for friction control.
Circular economy
- Recycling titanium scrap to high-end powder for AM
- Designing refractory ceramics using steel industry by-products as the base
- Utilising mine tailings as a feedstock of ceramic injection moulding
Novel 3D printed solutions with tailored powder materials
Tailored powder materials such as soft magnetic materials enable the creation of new innovative additive manufacturing solutions, thus bringing the power of topology optimization to new applications. An example of this is VTT’s work in developing a 3D printed electronic motor.
Versatile powder-based materials offer a world of possibilities when it comes to modifying the properties of base materials.
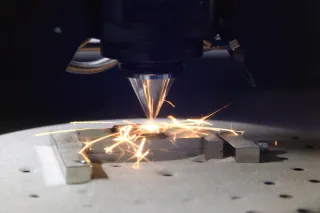
Manufacturing with Multimaterial Laser-Based Direct Energy Deposition System
Unlock the future of material development with our state-of-the-art laser-based direct energy deposition system. Featuring co-axial powder feeding that can handle up to six different powders simultaneously, this system is designed to push the boundaries of innovation.
Key Benefits:
- Multi-Material Capability: Demonstrate complex multi-material samples and simple components with ease.
- High Throughput Alloy development: Accelerate your experimental material development with unparalleled efficiency.
Utilize the next level of manufacturing technology and stay ahead of the competition. Transform your ideas into reality with our cutting-edge solutions!

Driving business impact through science-based sustainability solutions
Many companies have set themselves ambitious climate commitments and sustainability goals. VTT PowderPiloting looks for ways to support your environmental efforts while preserving your bottom line.
Here’s some ways we can achieve that:
Circular economy
- Designing forward-looking solutions based on alternative raw materials
- Finding ways to utilise secondary materials and industrial side-streams
Coatings
- Designing cost-efficient solutions against wear, corrosion and high temperatures
- Tailoring material properties to fulfil the performance criteria of harsh operation environments
Components
- Designing high-performance components using cost-efficient and sustainable manufacturing methods
- Designing durable and reliable multimaterial components
- Tailoring components to meet the highest demands and standards
Functional additives
- Graded or locally reinforced structures, added functionality like integrated catalytic properties or electro-magnetic properties
VTT’s exceptional research infrastructure - from powder manufacturing to powder consolidation to post treatment and characterisation
Powder manufacturing
- Gas atomisation
- Spray drying
- Plasma spheroidisation
- Mechanical alloying and mixing
- Powder classification
Powder consolidation
- Additive manufacturing (AM)
- Hot Isostatic Pressing (HIP)
- Powder Injection Molding (PIM)
- Self-Propagating High Temperature Synthesis (SHS)
- Thermal spraying
- Laser cladding
Post treatments and characterisation
- Heat treatments
- Surface treatments
- Performance testing and validation
- Powder characterisation and usability analysis
Powder piloting - Upscaling partnership model
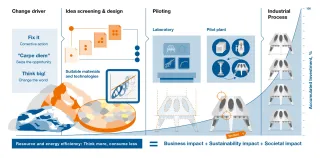
How to work with us
-
Contact us!
Tell us what you want to do, and we will figure out how to do it. After the initial assessment, we can proceed with one of the following options. -
Customised partnership
Every research case is unique, and we’re happy to tailor our services to your needs. We’ll take you from idea to prototype without hassle. -
Cooperative project
We frequently participate in research and development projects with multiple business partners and funding agencies. In cooperative projects, the risk is split between multiple organisations and everyone benefits from the results. -
Our networks at your disposal
We are happy to put you in touch with the ideal sparring and development partner.
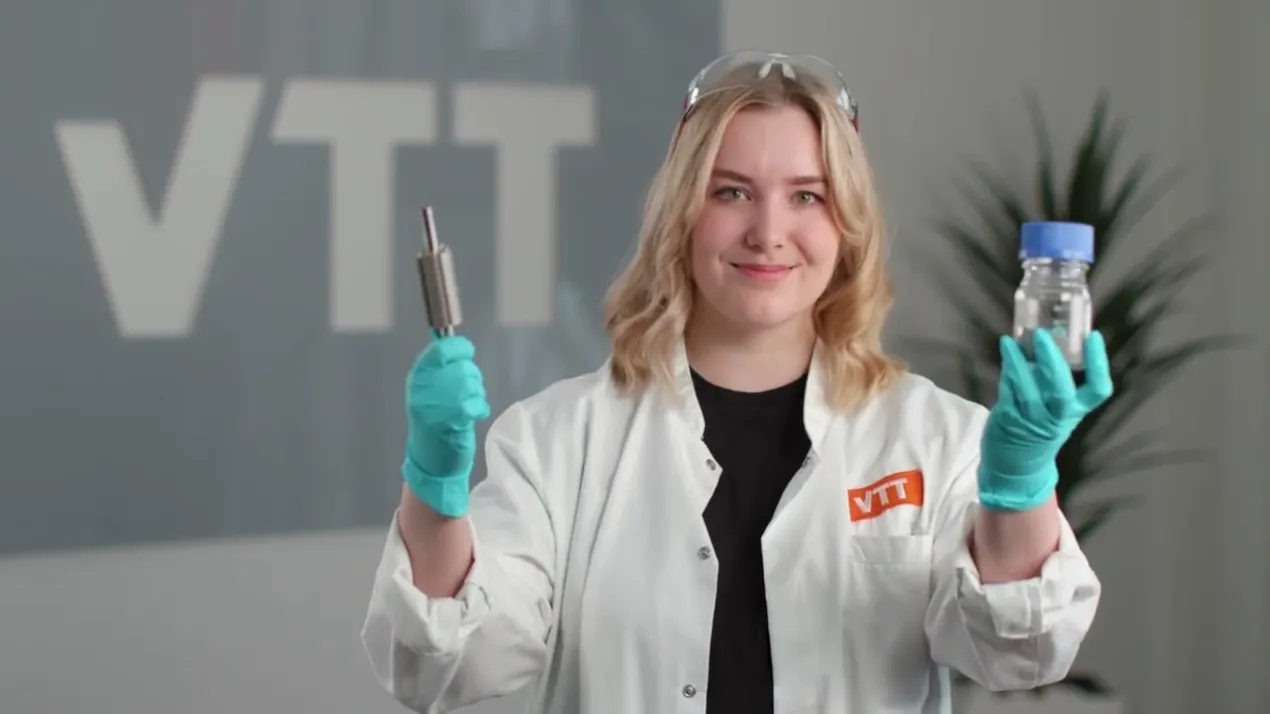
Contact us here!
Digitalising and 3D printing spare parts enables manufacturing anywhere and anytime
The digitalisation of spare parts is a step towards more sustainable business and reducing the carbon footprint of industry. VTT and Aalto University have been conducting research to promote digitalising and 3D printing spare parts.
