Chemical process technology
Our chemical process technology infrastructure is built to support companies and research partners in developing and piloting sustainable chemical processes. The facilities can be used for research and innovation projects from laboratory to pilot scale with a wide industrial application range.
Our facilities, on-site analytics and related scale-up competences enable faster product development and lower costs for the scale-up phase. This is made possible by utilizing our extensive expertise in various materials and their production processes together with our ability to combine material, process and analytical knowledge in a scientific way.
Typical projects focus on solving scale-up challenges related to processing and modification of renewable and recycled materials, and on finding innovative reuse and recovery of side and waste streams. We have unique pilot facilities and a recognized team with decades of competence in collaboration with industry and universities and institutes from different sectors. We operate focusing on safety and quality.
Our key infrastructure and competences:
Multi-purpose process chemistry pilot plants in Espoo (Bioruukki) and Jyväskylä to support research, development and scale-up in:
- Process piloting for new functional materials derived from renewable and recycled sources
- Future separation and recovery technologies
- Advanced upgrading of renewable and recycled feedstock
Our infrastructure is composed of various size and type of equipment that can be customized for purpose to handle materials from kg to ton level:
- Reactors
- Multi-purpose agitated stainless steel reactors
- Multi-purpose agitated glass lined reactors
- Bench scale high pressure reactors
- Bench scale pipe reactors
- 4-folded high-throughput hydrotreatment reactor unit for hydrogenation and isomerization
- Lödige multiphase reactors
- Fed batch distillation pilot unit
- Counter-current extraction column
- Powder dry mixing unit, grinders, in-line mixing
- Solid-liquid separation
- Separation with decanter centrifuges and disc stack separators
- Nutsche type pressure filters
- Pressure filtration
- (Vacuum) belt filtration
- Cartridge and bag filters
- Screw press
- Decanters and centrifuges
- Membrane separation
- Pressure driven membrane filters; dead-end and cross flow
- Membrane contactor, membrane distillation and forward osmosis systems
- Electrodialysis systems
- Spray and freeze driers
- Resource container for mobile testing of different unit processes
We provide:
- Scale-up data for early validation of technical and economic feasibility
- Critical data and material production for ensuring products match requirements
- Scaled-up process data for detailed process engineering, investment decisions and operating costs optimization
- Separation and recovery concept creation and testing
- Testing of key technology alternatives for creating scale-up design basis
- Proof of concept demonstration and material production
- On-site customer testing support with mobile equipment with selected separation unit processes
For whom:
- Chemical process industry
- Pulp and paper industry
- Energy industry (fuels and batteries)
- Mining and metals refining industry
- Food industry
- Start-ups, SMEs and RTOs

Process piloting and advanced upgrading of renewable and recycled materials
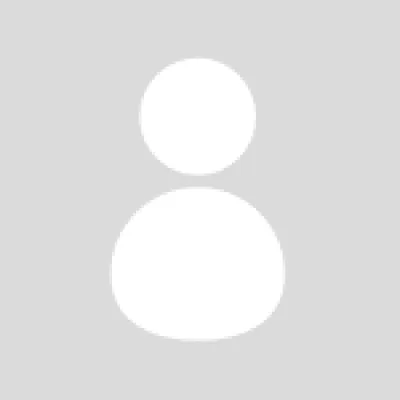