Scorching hot plasma, temperatures colder than cold, mega-heavy components, and finely tuned, delicate technology—all within fusion reactors, hailed as the future of energy production. One of the challenges of implementation relates to something as mundane as maintenance: how to dispose and replace worn parts in hazardous and extremely challenging conditions? VTT tackles maintenance of radioactive plant elements with the new Remote Handling Control System demonstrated by Senior Scientist Jarmo Alanen and his team.
Within the ITER reactor, the world’s largest fusion reactor experiment located in Southern France, hydrogen isotopes deuterium and tritium fuse at high temperatures, producing superheated plasma. This plasma is contained by powerful superconducting magnets in a doughnut-shaped tokamak chamber.
Although ITER is not intended to produce electricity, it paves the way for reactors that can. As fusion occurs, it releases substantial energy in the form of high-speed neutrons and charged particles, heating the plasma. The heat would be captured by the reactor wall blankets, facilitating steam production to power turbines for electricity generation.
While plasma is ten times hotter than the sun, superconductors require close to absolute zero temperature to function.
“This contrast perfectly demonstrates the extreme conditions that set specific demands for running a fusion plant. One of the direst challenges to solve is maintenance, and that’s where the Tampere Divertor Test Platform 2 site comes in”, says VTT’s Senior Scientist Jarmo Alanen.
Demanding conditions call for remote maintenance
It is fair to say that fusion plants could not exist without remote maintenance. Worn-out plant elements need to be replaced and nuclear dust must be removed and handled safely. Jarmo Alanen and his team are experienced in remote handling under extremely demanding conditions. Their dedicated robot, Cassette Multifunctional Mover, maintains the massive ash tray laying at the bottom of the tokamak chamber – the divertor.
“The good news is that the fusion plant elements and the nuclear waste stays low-level radioactive for only about 100-200 years against the 100 000 years associated with the spent fuel of fission. But of course, during the lifetime of the power plant, we still need to play with highly radioactive particles and elements to keep the plant operational,” Alanen explains.
The helium ash and impure particles peeled off from the wall of the reactor by the nuclear reaction are gathered into massive divertor cassettes located at the bottom of the reactor. As one cassette weighs approx. 10 000 kilos, removing one requires a robot of an equal weight to navigate in a narrow maintenance tunnel. Moving large masses with a half-millimetre precision is not a simple feat.
To solve the challenge, Fusion for Energy, VTT, and Tampere University initiated a collaboration to develop and integrate ITER’s Remote Handling Control System at the DTP2, the divertor test platform located in Tampere. The project is a demonstration of a successful partnership between applied science and companies: VTT developed a virtual 3D environment and remote diagnostics application that are accompanied with GTD’s Command & Control system, Genrobot robotics software, and an LLC communications system driver.
The system controls the robot, and predicts and monitors for possible issues, halting all movement should a collision, for example, look likely. To do that, RHCS also uses 3DNode, a camera-based tracking system from Tampere University, to track the exact position and orientation of the target in situations that require impeccable accuracy. DigiValve, another Tampere-based innovation, plays a key role in the hydraulics behind the robot’s movements.
In January 2024, Alanen’s team demonstrated the ITER compliant Remote Handling Control System for the first time to its partners and collaborates.
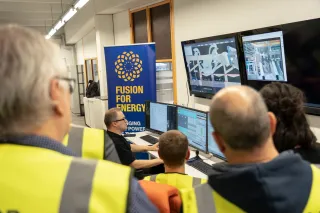
“While the operator can more or less rely on pre-taught trajectories, they may need to manually control the robot. Sometimes slight moves are needed, especially due to the tight fit of the robot-cassette interface or to compensate for deflections when lowering down the 10-ton load. The required simultaneous sideways movement and rotation one millimetre at a time without camera view is quite a task. The virtual reality model and virtual instruments provided by C&C are crucial,” Alanen says.
Of course, replacing divertor cassettes is not the only task in maintaining a fusion reactor. But the conditions are often dangerous and inaccessible to people. Alanen’s team studies various smaller robots to weld, vacuum, tighten bolts, and open or close doors inside the radioactive reactor. Many of the tasks are delicate in nature, and excessive force could lead to dire consequences.
“A haptic controller informs the operator about the tactile sensations of what the robot under their control is doing. While automation brings increased efficiency, some tasks still require humans. Robotics can be of great help in extending our capabilities and making maintenance safer,” Hannu Saarinen, a Senior Scientist at VTT sums up.
Innovations of applied sciences give companies a competitive edge
As fusion reactors are sensitive for any impurities, the remote maintenance system utilises water-based hydraulics – something Tampere has extensive expertise in since the 80s’. The digital valve, DigiValve, is a unique innovation from Tampere University of Technology, Fluiconnecto and Tamlink, that promises increased reliability for demanding environments.
“The servo valves used initially for the remote handling system proved less ideal, as they wore off easily and were prone to blockages. DigiValves are far more resilient against failures, as the system of 16 on/off valves does not rely on one valve alone like with the old solution. They are easy to control digitally and offer better performance and very accurate tracking,” Alanen says.
Another innovation, camera-based tracking system 3DNode, measures the coordinates and rotation angles of the divertor cassette from the markers placed on the maintenance tunnel and the cassette to calculate the robot’s position. There are commercial machine vision solutions, but none that would cater to ITER’s constraints such as material properties and the low resolution of rad-hard cameras.
These innovations are a great example of applied sciences and companies working together to create solutions with wider commercial possibilities. A fusion reactor is likely the most demanding environment for water hydraulics, but the same technology could be used in other industries that need to move large masses with high precision.
Construction, manufacturing industry, and transportation are only a few examples that could benefit from solutions developed for ITER’s remote handling needs. Harnessing the expertise required for a fusion reactor to become a part of our everyday lives is possible already today.
Jarmo Alanen happy after a successful installation of the divertor cassette.
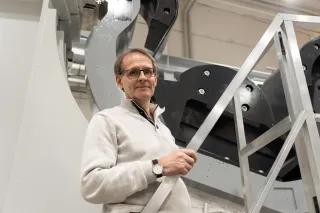
F4E-GRT-0901 Project Facts
- The project has received EU funding via Fusion for Energy (F4E), the organisation managing Europe’s contribution to ITER, plus contributions from VTT and Tampere University.
- The Project has been coordinated by VTT.
- The main milestone of F4E-GRT-0901 was the demonstration of the ITER Remote Handling Control System at F4E Divertor Test Platform (DTP2) hosted by VTT in Tampere, Finland.
- Under the grant, VTT has provided the Remote Diagnostics Application and Virtual Reality, and Tampere University the 3DNode camera-based pose measurement system.
- GTD, Tamlink and Fluiconnecto have also contributed to this area of work via other contracts signed by F4E; GTD with Genrobot, Command & Control, and LLC communications software; Tamlink and Fluiconnecto with DigiValve water hydraulic digital valve. These all together with VTT and Tampere University contributions were experimentally validated under F4E-GRT-0901 at DTP2.
- F4E has carried out the technical coordination between F4E-GRT-0901 and the other contracts.
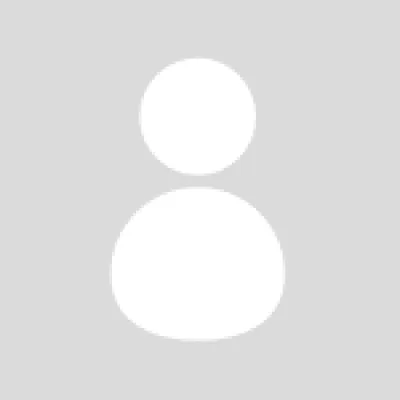