The first plasma-FIB scanning electron microscope in Finland has just become operational at VTT in Espoo, Finland. This multi-million investment will significantly contribute to Finnish materials research for applications such as hydrogen economy, microelectronics, and the marine industry, as well as to material damage investigation.
A TESCAN AMBER X system, Finland's first Focused Ion Beam (FIB) Scanning Electron Microscope (SEM) using Xenon plasma, has been taken into use at VTT Technical Research Centre of Finland. In the Nordic countries, there are just a handful of similar systems that are rare worldwide.
The multi-million priced equipment includes all the bells and whistles that a materials researcher could dream of. Compared to traditional FIB-SEMs, it provides huge potential for excelling in materials research and multiplying the speed of materials development.
“The new capability for lightning-fast materials characterization in 3D supports, for example, integrated computational materials engineering (ICME) and materials acceleration platforms (MAPs). While new materials traditionally take ages to develop, this capability allows us to reduce the time from design to market roughly to one-tenth,” says Supriya Nandy, Senior Scientist at VTT.
State-of-the-art materials development for industry needs
The new FIB-SEM is designed to perform site-specific investigations with nanometer accuracy for all types of materials, such as ceramics, metals, and even soft materials like wood and paper. The sample can be imaged and tested simultaneously, which is useful, for instance, for observing how the material reacts to a certain load.
“With the help of plasma-FIB and its in-situ testing capabilities, we can answer questions not only about the material’s properties but also about how the material behaves under strain, extreme temperatures — or both at the same time. What else could a materials scientist dream of when developing state-of-the-art materials for current and future industry needs?” Nandy continues.
The TESCAN AMBER X at VTT provides several Finnish industries with opportunities for groundbreaking materials development.
“Marine and aviation industries could benefit from our equipment to ensure their materials will always endure in various conditions. Another example is the emerging hydrogen economy, which requires careful studies and analysis of surface materials. Also, the battery and semiconductor industries could be very interested,” says Janne Pakarinen, Research Team Leader at VTT.
In addition, VTT will use the new FIB-SEM in material damage investigation, for instance, for chemical, paper, and marine industries. Samples can be scanned very accurately to see possible deformations in crystal structures.
“We receive assignments to find the root cause of material failures. It is particularly important to investigate the failure mechanism in materials to avoid repeating similar damage in the future,” Pakarinen says.
Xenon brings a decisive advantage compared to gallium-based FIB-SEMs
The new equipment at VTT operates using xenon plasma instead of gallium, which is used in more traditional FIB-SEMs. The maximum range of Ga-based units is a hundred nA, whereas the Xe-plasma-FIB can do several µA ion currents. This difference is crucial and enables considerably better possibilities for research.
“The plasma-FIB's ion-milling process is extremely fast and allows for significantly larger cross-sections and volumes to be investigated compared to traditional ion milling. Unarguably, this gives a more complete understanding of the materials’ properties, increases the sample throughput, and improves the possibilities, for example, in materials modeling that is based on or benchmarked always with experimental data,” Supriya Nandy explains.
In addition to the plasma-FIB, the new SEM comes with state-of-the-art detectors for Energy Dispersive Spectroscopy (EDS) and Electron Back-Scattering Diffraction (EBSD) and in-situ tensile stage that can reach up to 1200 °C.
The system has been fully operational since mid-March.

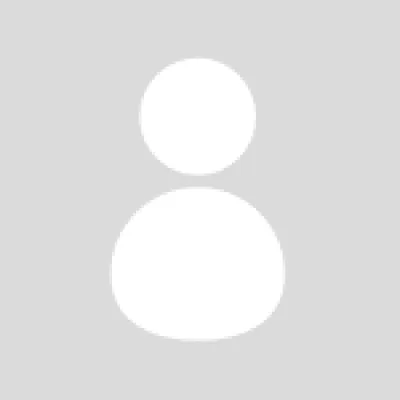