Printed electronics
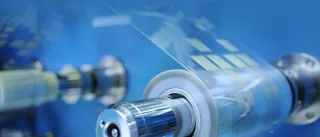
The environmental load of the electronics industry can be significantly reduced by moving from traditional manufacturing processes to printed electronics and from fossil-based materials to bio-based materials. VTT has unique capabilities to make this a reality: sustainable electronics know-how, roll-to-roll printing and hybrid manufacturing technology for flexible electronics, and a printed electronics pilot factory with 20 years of experience and over 100 experts.
Key facts
We have a unique combination of over 100 multi-technological experts and a world-class printed electronics pilot factory.
We can support our customers in different projects including or combining sustainable electronics, flexible electronics, and structural electronics.
We are working with almost 100 companies from 4 different continents annually in contract R&D and more than 200 companies in jointly funded projects.

Industries that rely on electronics are facing a novel challenge: how to deal with scarcity of resources while also managing rising volumes of electronic waste. Overcoming the challenge calls for new, sustainable approaches. At VTT, we have expertise and research infrastructure that allows us to support our customers in creating, developing and commersialising advanced flexible, printed and hybrid electronics that increase both the sustainability and the performance of new product concepts or existing products and solutions.
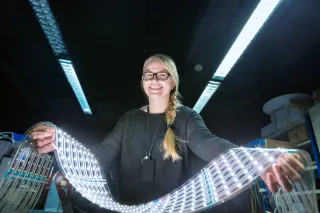
Printed electronics – making sustainability the new normal
At VTT, we want to make sustainable materials the new normal in electronics.
As a strategic partner to our customer, we develop electronics sustainably through multidisciplinary competences in bio-based material development and printed and hybrid electronics. Our combination of expertise allows us to develop tailored solutions for complex applications. We can support in boosting sustainability through the full lifecycle of electronics, including:
- Product & component ecodesign
- Sustainable materials
- Sustainable usage & disposal
- Energy- and resource efficient processes
We know from successful experience that sustainable electronics have the potential to create new business for electronics and optics industry, while drastically reducing its environmental burden.
We meet our customers where they are at. Whether you need an early roadmap, a targeted analysis, a new prototype, process development in pilot lever manufacturing or support in commercialisation, we are able to help you take the sustainability leap and start manufacturing electronics devices that are compatible with circular economy.
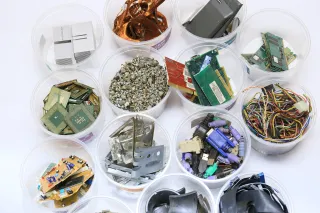
Flexible electronics
Current electronics products are basically rigid circuit boards inside rigid boxes. VTT Printed Intelligence provides solutions for electronics that are flexible, soft, conformable, and even stretchable. They can, for instance, measure various parameters from a human body such as temperature or heart rate, and be worn as patches – much like intelligent bandages. These flexible and even stretchable electronics with novel form factors can be used for instance in diagnostics and wellness applications.
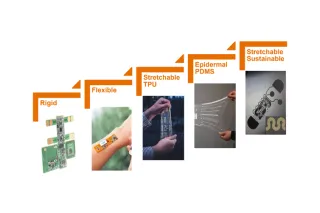
Case: Printed electronics drive innovation in health technology
VTT partnered with GE Healthcare to develop a next-generation wearable sensor for patient monitoring. This lightweight and user-friendly solution enabled by printed electronics can offer a convenient and affordable solution to support patients in recovery after illness or medical procedures.
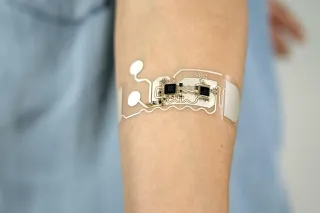
Structural electronics
Structural Electronics is a novel way to seamlessly integrate electronics into different materials and structures from car interior lighting to displays inside plastics or glass windows, or other materials/structures. Reducing the need of material usage and product weight, structural electronics has a high impact in sustainability and eco-efficiency in various applications. Structural electronics create opportunities for new applications in many industries including automotive, construction, and infrastructure.
In structural electronics approach, the functionalities of the system – electronics, photonics, and mechatronics – are seamlessly integrated in the mechanical body. The result is a self-supporting, highly integrated, robust, and functional product.
Benefits from structural electronics:
- Reduced complexity - less mechanical parts and single substrate implementation
- Reduced volume on system size, thickness, and weight
- Seamless integration - combined optics, electronics, and mechanics
- Design freedom with 2D and 3D geometry
- Novel large area product architectures – enabled by Roll-to-Roll, Roll-to-panel -manufacturing
- Greener electronics – additive manufacturing, less material usage, better environmental sustainability
- Simplified value chain – less subsystems and suppliers and logistics handling by rolls of components
Successful spin-offs show the business potential of printed electronics
Printed electronics technologies developed at VTT have played a crucial role in creating commercial success. We look forward to helping build more success stories with you.
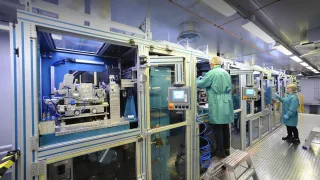
TactoTek
TactoTek, which is a leading provider of solutions for Injection Molded Structural Electronics (IMSE), currently operates on three continents and has 100 employees. VTT's research and development work is behind the IMSE technology, which reduces assembly costs by more than 30% compared to traditional manufacturing methods.
Dispelix
Dispelix is an advanced waveguide designer and manufacturer delivering next-generation visual solutions for consumer and enterprise AR and MR wearables. The company’s technology is based on photoconductor optics developed by VTT, which enable the manufacture of displays in the form of light and thin elements, with a thickness of just one millimetre, on either glass or plastic.
Unique know-how and world-class pilot factory
VTT offers a unique in-house competence from material formulation and process development of pilot-scale roll-to-roll production to multi-technological knowledge of applications and systems. We also have a world-class, award-winning roll-to-roll capable pilot factory for printing, component assembly and post processing.
We offer R2R prototyping, verification, piloting and up-scaling services for new material, process and product concept developments for large area and flexible form factor electronics, photonics and bio-µsystems. We can, for instance, assemble tiny ICs and print circuits with conductive inks on flexible and stretchable even biomaterial and paper-based substrates in a continuous roll-to-roll process to a proof-of-production level.
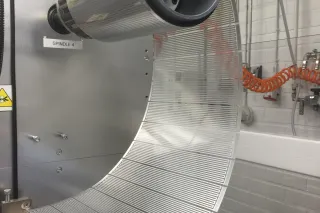
PrintoCent – industry cluster for printed electronics
VTT initiated the PrintoCent ecosystem in 2008 to boost the commercialisation and industrialisation of Printed Intelligence. The PrintoCent ecosystem has created 30 start-ups since 2011 and has 400 employees in companies. Up till today, the investment to companies is around 50 M€. At the very core of the activities is the International Industry Cluster of 40 member companies, ranging from automotive, ICT, diagnostics business sectors and respective value chains, who are working with us to exploit the opportunities of Printed Intelligence.
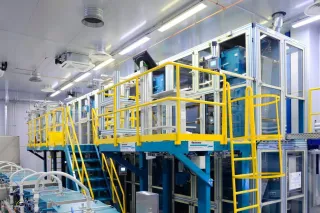
How to work with us
-
Get in touch with us! Starting with the first contact, we are committed to understanding your business and goals, and working out how to best support you.
-
Typically, work with us begins with a proof-of-concept. This allows us to fully understand and test the best ways to respond to your challenge.
-
With a proof-of-concept done, we will focus on manufacturing process development. In this stage we develop and proof the key manufacturing process steps in our pilot factory, and/or with collaboration with our partners.
-
Once verifications and measurements have been completed, it is time to move to ramp-up, technology transfer and toward commercial applications. We support the transfer to customers, their supply chain or to carefully selected manufacturing partners.
Contact us here!
See our publications
VTT Webinar: Circular design for electronics
How to design sustainable and circular electronics to fit the new EU requirements? What is required to build a techno-economically feasible route for sustainable recycling of the materials at the end of their lifetime? How to ensure lean manufacturing with minimum waste and emissions?