VTT’s world-class piloting facilities and extensive experience in foam forming solutions offer a path to bio-based material innovations. For example, sustainable plastic-free multilayer air filter materials can be produced at pilot scale using stratified foam forming. Foam forming makes it possible to produce new, high-performing sustainable products with small changes to the customer’s current production lines.
There is increasing demand in various businesses – including packaging, hygiene products, filtration and construction – for replacing fossil-based materials with bio-based alternatives that are recyclable and biodegradable. However, many current manufacturing processes have limited capability to handle different raw materials.
Foam forming is an adaptable technology that can be used to produce unique structures using a range of bio-based materials. VTT has been creating and piloting foam forming solutions for over 15 years and has state-of-the-art facilities that can be tailored to the needs of each customer.
“The benefits of foam forming compared to traditional methods include the possibility to adjust porosity and bulkiness and use longer fibres, and a wider range of raw material combinations. The technology also provides good formation and highly consistent results with better productivity, for example, compared to other nonwoven and textile processes,” says Jaakko Asikainen, Research Team Leader from VTT.
Share of plastic fibres decreased substantially in multilayer filter production trial
Air filtration is an example of a strongly growing business that can benefit from utilising foam forming to produce alternatives to current plastic-based air filter materials. VTT has carried out pilot trials for manufacturing a multilayer air filter using stratified foam forming.
“Good layer purity and the possibility of applying long staple fibres – still maintaining good sheet formation – can be achieved with stratified foam forming. This method of forming layered products with a single headbox can simplify tissue, paper and board machinery, and considerably lower the cost and size of a machine,” Jaakko Asikainen explains.
The viscosity of foam is 1-2 orders of magnitude higher than that of water, which enables the generation of high layer purity in stratified forming. The method also enables gradient structures and precise chemical dosing by foam layer.
The bulky fibre structures created in the trial were strengthened with conventional dry and wet strength aids. Only about 20% of polypropylene fibre content was required to reach the filtration efficiency of commercial filters made of 100% plastic fibres. For the efficiency level, the sheet was electrically charged, a procedure that also gives the required performance to commercial filters.
Modular platform and customisable partnership
VTT’s pilot lines are highly adaptable research platforms for fibre products of the future. They are easy to modify, with design and construction support provided by our experts, offering our customers a cost-effective solution. Considering foam forming, the additional features of VTT’s pilot lines simplify the process of forming on a web by enabling the feeding of the continuous web into the headbox. Also, composite structures can be produced in a single step by utilising the machine’s dry particle feeder.
With VTT’s help, you can optimise raw materials, processes, and product properties. With the support of our experts and customised production processes, you’ll be able to expedite the upscaling of production and widen your product portfolio with value-adding sustainable options.
Specialised foam forming pilot lines
VTT’s laboratories and two modular piloting platforms (SUORA and SAMPO) located in Jyväskylä, Finland, offer excellent facilities and skilled personnel for development work and the scale-up of new technologies, raw materials, process concepts and chemicals:
The SUORA machine consists of forming and pressing sections and reeling and is able to run both foam and water-laid webs.
As the manufacturing line of highly porous products cannot include a wet press, the SAMPO pilot line was custom-made for foam forming with the aim of being able to produce also bulky and soft low-density materials on a pilot scale. It includes both vertical and horizontal headboxes, non-contact air impingement and through air dryers (TAD).
Explore our infrastructure
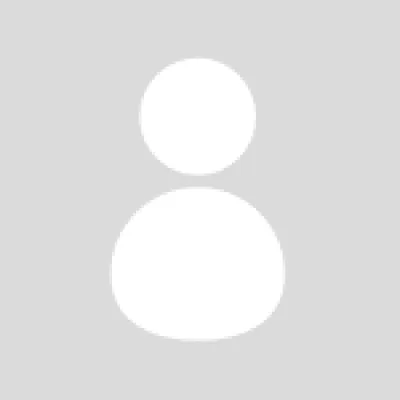