Valmet and Metsä Group’s innovation company Metsä Spring wanted to design a new production line for novel 3D wood fibre products that could replace traditional plastic. VTT expedited the design and validation of the new production line and process. VTT and Valmet’s collaboration resulted in a demo production line for a versatile alternative to plastic.
Key facts
Novel 3D fibre products that tackle climate change and plastic challenges
Fast and high-quality design project for an efficient and automated production line
Reduced time to market with agile piloting and validated design choices
With a history of over 200 years, Valmet is a global developer and supplier of process technologies, automation and services for the pulp, paper, energy and marine industries. The company’s net sales in 2020 were approximately 3.7 billion euros. Valmet’s shares are listed on Nasdaq Helsinki.
3D wood fibre products have potential to replace plastic
With rapidly rising global plastic production volumes, international regulation is increasingly focusing on the reduction of single-use plastics. Increasing environmental awareness among customers and tightening regulation have led businesses to create new solutions that could offer a sustainable and versatile alternative to fossil-based plastics.
Single-use packaging is, however, necessary for various purposes. To introduce new, sustainable packaging solutions, Metsä Spring, the innovation company of the Finnish forest industry group Metsä Group, wanted to establish a greenfield demo production line for the development of 3D wood fibre products. Valmet was chosen to develop and design the new line.
“A functioning recycling ecosystem for wood fibres is already in place. The goal was to create a production line for novel, sustainable wood fibre products that would differentiate the company from the current competition in the field of moulded fibre products,” says Sampo Immonen, Head of Line R&D at Valmet.
The project’s schedule and goals were both ambitious. Valmet had to develop various new pieces of equipment and validate their effects and interaction in the production process.
To complete the new production line successfully and on time, Valmet had to identify and fill their own knowledge gaps with partners that have both experience and expertise. Valmet did not have the time to build their own test equipment and do extensive research on every aspect of the design process. This was when Valmet turned to VTT.
R&D, test equipment and fibre expertise make the difference
Valmet knew that VTT is a global pioneer in special fibre suspensions, a field which is integral for the new production line.
VTT first supported Valmet on specific lab research and equipment design, and by providing suitable test equipment. Later, VTT’s team tested the demo production line’s operation and functions. In addition, VTT supported Valmet on:
- mould and material testing
- dimensioning
- verification of equipment choices
- chemicals
- production processes, especially regarding fibre suspensions
The partnership gave Valmet invaluable information about how small details affect the whole production process. “VTT has unique wood fibre know-how that cannot be found anywhere else in the world. For our project, they also had the test equipment and research knowledge that validated our production process,” says Immonen.
With VTT’s support, Valmet finished the demo production line on schedule. “VTT’s experienced researchers and their strong expertise on piloting were essential in reaching our targets. There was no need for an extensive trial-and-error period during development, which expedited the whole development process,” Immonen continues.
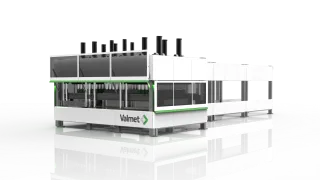
3D fibre production line enables sustainable packaging products
The benefits of the project are significant.
Metsä Spring now has a 3D fibre production line that:
- tackles climate change and plastic challenges by replacing fossil-based plastic
- enables high-quality, sustainable packaging products
- multiplies production rate compared to currently available MFP machines
- has a high automation rate, low production costs and an efficient supply chain
The production process and the product quality parameters are also being further fine-tuned with Metsä Group’s potential customers.
Valmet and VTT strengthened their expertise in developing cutting-edge production processes on a tight schedule. The successful project also validated that the partnership reduced time to market and project risks.
Roope Siilasto, VTT’s Research Team Leader, is impressed with the project: “The partnership with a global leader like Valmet was hugely beneficial for our organisation, too. We further improved our expertise on wood fibre solutions. Researching, designing and validating a new, innovative production process deepened VTT’s know-how from R&D to implementation.”
Defining added value paves the way for future collaboration
The agreement was based on the added value that Valmet gained. “In blue ocean innovations, it’s often hard to accurately define the scope of services required from development partners. We truly appreciated the open discussion about our goals and doubts regarding the project. We agreed on certain metrics that would define the added value VTT brings, and based the pricing on those metrics,” Immonen concludes.
Jaakko Kuusisaari, Customer Account Lead at VTT, also underlines that transparency enabled a smooth and efficient collaboration: “The key was to identify the areas where our expertise supports Valmet best. VTT and Valmet have already collaborated in various fields over the years. This project further strengthens the mutual respect and trust between the organisations and builds a solid foundation for future innovation projects in multiple areas.”

